ERP for Manufacturing: Consolidate and Organize Data Better Than Before
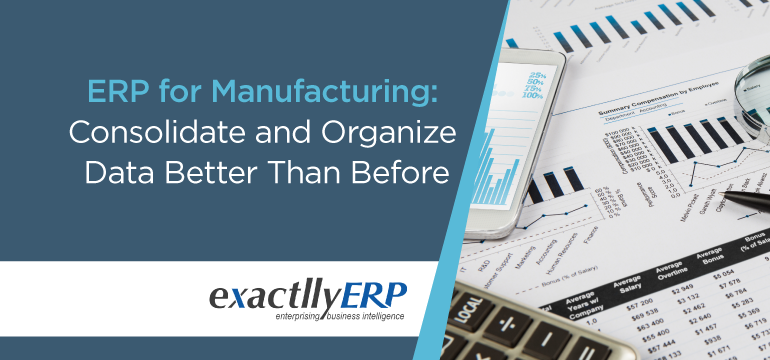
Manufacturing processes need constant vigil. The production line is always on. One has to maintain a non-stop production without any process obstruction to meet delivery schedules. The customer delivery schedule can be met only if you are able to achieve high operational efficiency. A production line can be hindered because of various reasons like defective production, shortage of raw material, overproduction (leading to storage problem and damage of finished goods), machinery breakdown, inefficient workforce etc.
Problems faced due to lack of Automation in Manufacturing:
When the scale of production and number of customers become high, there is a huge amount of data collected on a daily basis. Manual data entry becomes an arduous task for your workforce and data access seems like a distant possibility. It is not only time-consuming but loaded with human errors. Many manufacturers have basic software in place for accounting, inventory management etc. Some of them only use manually driven excel sheets. But such software only solves half the purpose by delivering semi-automated data. There is hardly any control over data as data mining and processing is difficult. Furthermore, there is poor coordination among different departments due to a lack of real-time data communication. This causes poor visibility into overall operations.
The problem of data management aggravates with the growing complexity of business operations. Business units scattered across different locations have a major problem in consolidating data. Every location has its own information silos with different data structures. The rising complexity of manufacturing businesses can also be witnessed when the business involves multiple currencies, multiple borders (both global customers and operations) and rising customer specifications. The data takes a complex form that can only be managed through a consolidated solution namely ERP.
Data Consolidation is the way forward:
ERP is just the right software solution that helps manufacturers to gain expertise in complex tasks like just-in-time inventory and six-sigma methodology. Six-sigma is completely data-driven and with solid control over data you can refine your product quality and minimize defects. ERP is a complete solution for the manufacturing enterprise.
Managing inventory was never so easy. The raw material and finished goods inventory is reflected in the ERP system in real-time and the production department can plan the production schedule and order raw material. Multiple vendors for different raw materials can be managed smoothly as vendor data is stored in the system with priority vendors marked out. Payment and credit schedule for different vendors is easily visible. Similarly, ERP manages customer data helping you to identify and maintain long-term relationships with key customers. Customer address, previous orders and customer purchase history are all stored in the system. Order management allows the customers to track the order status. It also helps the sales executives to know pending orders and priority orders.
Conclusion:
Manufacturing can be labour-intensive for no reason. With automated machinery and processes, the need for labour should be reduced. Some manufacturers still prefer to keep more labour than required to manage the production because there is no control over data. With clear visibility into all aspects of the production line, ERP empowers the production staff to take better control of data.
ERP allows you to maintain data in a centralized database. The data can be easily analyzed and reports can be generated to give insights related to production, inventory, customers etc. The reports make interpretation easier and help to propose a suitable solution. Thus, ERP should be implemented to increase productivity and reduce cost with real-time control over processes.
exactllyERP is one of the most advanced ERP software providers present in the industry. Feel free to Contact Us and get a Free Demo.